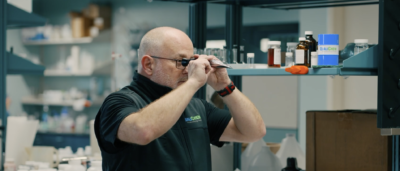
How to Correctly Use a Refractometer
When it comes to metalworking fluids, consistent and accurate concentration control is crucial.
When coolants are used properly, customers can realize their full benefits, including increased tool life, superior surface finishes, and reduced consumption. To do this, it’s very important that the metalworking fluids are maintained in the correct concentration range.
A refractometer is the tool needed to measure concentration on the shop floor in machining and grinding applications. In very simple terms, refractometers measure how much “stuff” is in the water. The “stuff” in the water is the concentrate that users mix with their water to create a coolant. Refractometers do not “see” the water.
Customers buy a concentrate and create the coolant by diluting the concentrate with water. The ratio of water to concentrate, or the “concentration” of the coolant, is important because that’s how parameters, such as cutting or grinding performance, stability in the sump, and corrosion, are maintained.
Refractometers 101
Why are refractometers important? Because the concentration of your water-diluted metalworking fluid (coolant) is important. Whether you are using soluble oils, semi-synthetics, or full synthetics, concentration is critical.
Coolants are designed to keep you productive while controlling a host of potential problems, including rust, bacteria, residues, and foam, during the machining or grinding processes. All coolants are designed to run within a minimum and maximum concentration range. Refractometers are the tools to help ensure that the coolants are in the correct range of concentration.
What type of refractometer should you use? There are two handheld refractometers for use on the shop floor: analog and digital. Most maintenance personnel and machinists are familiar with the analog refractometers: flip-up lens cover, add a drop of coolant, close the lens cover, look through the eyepiece and read the scale. Digital refractometers do most of the work for you: a drop of coolant on the optical sensor, and the unit provides a value.
Calibrating Your Refractometer
Like all the other gauges in your shop, you must make sure you’re measuring with a calibrated refractometer. Whichever type of refractometer you select, we suggest using one that can be calibrated.
When calibrating a refractometer, it’s imperative to calibrate the refractometer with the same water you’re using to mix your coolant. Everyone’s water is different, but you’ll want the refractometer to read “0” with your specific water BEFORE measuring the concentration of the coolant.
To calibrate an analog refractometer:
- Lift the lens cover and put a sample of the same water you’ll use to mix the coolant onto the lens
- Lower the lens cover
- Look through the eyepiece to ensure that the scale reads “0”
- If it does not read “0,” adjust the calibration screw (usually located on the bottom of the refractometer) until the scale reads zero.
Calibrating a digital refractometer is even simpler:
- Open the lens cover
- Place a sample of the water you’ll use to mix the coolant on the lens
- Follow the refractometer’s directions for zeroing the reading. The steps necessary for this process usually take less than a few seconds.
How to Read a Refractometer
Refractometers were originally designed for determining the concentration of sugar in wine. As such, the units on the analog scale or provided digitally are in Degrees Brix (or °Bx) and represent the sugar content of an aqueous solution. For the nerds: one degree Brix is 1 gram of sucrose in 100 grams of solution and represents the strength of the solution as a percentage by mass.
So how does °Bx translate to metalworking fluids? It does and it doesn’t.
Coolants are designed to be used at a certain percentage by volume. Hence the concentration for using a given coolant is quoted as a % by volume. However, refractometers don’t measure percent by volume on their own, they measure in °Bx . The °Bx must be converted to a % by volume.
Every coolant is different. The conversion from °Bx to % by volume can vary depending on how they are formulated. Every coolant will have what’s called a Refractometer Index (RI). This is the value that is used to convert °Bx into % by volume. The °Bx is multiplied by the RI to find the % by volume.
For some coolants, the RI=1, and therefore the °Bx = % by volume. For example, if you use a coolant with an RI of 1, and you measure the concentration in the machine as 7°Bx , then you know the concentration is 7%. This is the case with our XTREME CUT 250C: the RI is 1. When the RI=1, the coolant is said to be a “direct read,” so no conversion from °Bx to % volume is needed. The correlation is 1:1.
However, for many coolants, the RI is greater than 1. There can be many reasons why a coolant might have an RI greater than 1, but that’s a discussion for another day. Nevertheless, knowing the RI is important, especially when >1. Our Q-COOL 330C full synthetic has an RI of 3. So, in the example above, where the refractometer reads 7 °Bx, the concentration of the Q-COOL 330C would be 3×7, or 21%. In this example, the 330C would be significantly over-concentrated. You would normally want to see 330C with a °Bx of 1.5 to 3, or 4.5% to 9% after conversion.
The Refractometer Index should be reported on the Product Data Sheet or Technical Data Sheet for which coolant you are using. And along with the RI, the recommended range of % by volume should be listed for any given grinding or machining application type.
What type of refractometer do you need?
There are lots of refractometers out there that will do the job, so which is best? At QualiChem, we recommend the ATAGO Master-20M for those who prefer an analog unit or the MISCO PA201 for those who like digital. Both are very durable units and are easy to calibrate.
If you are using a coolant with an RI greater than 1, the choice of an analog refractometer should include a °Bx scale suited for the task. The ATAGO MASTER-20M has a scale from 0°Bx to 20°Bx. This unit works great for coolants with an RI equal to or less than 2, but the graduations between each whole number may not be fine enough for coolants with °Bx > 2. ATAGO also makes units with a scale from 0°Bx to 10°Bx.
In closing, refractometers help keep your coolant in great condition and help your applications perform the way they need to. The team at QualiChem is happy to help you with your metalworking fluid selection, use, and maintenance, including the use of a refractometer.